The Untouchables
The benefits of closed processing are well-documented, but what about the sustainability angle?
Rob Boulanger, Zach Page-Belknap | | 3 min read | Opinion
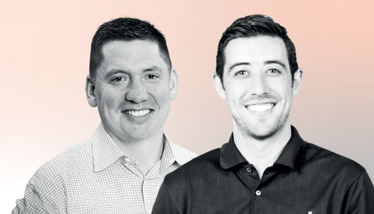
Credit: Authors supplied
When evaluating facility designs and meeting corporate sustainability goals, cleanroom environments and their supporting utility loads are typically treated as “untouchable.” Today, however, discussions of how closed processes could change these “untouchables” are on the rise.
A process designed to be closed offers the opportunity to reevaluate cleanrooms. A closed system isolates the process zone from the surrounding manufacturing suite and prevents the ingress of environmental contaminants during product contact. In addition to patient safety, removing the manufacturing environment as a potential source of contamination is advantageous when it comes to facility design and can lead to a reduction in biotech utility requirements. Closed processing improves both flexibility and efficiency, which can, in turn, help manufacturers meet their sustainability goals, reduce treatment costs and improve profits.
When evaluating a facility or facility design, a good starting point is a closure analysis risk assessment (CLARA). This is a systematic evaluation to provide the appropriate environment for each process step. Take a bioreactor suite with closed systems that have been validated to be closed and have continuous monitoring (e.g., vessel pressure, pH, DO, etc.) in place to ensure no process aberrations indicating contamination occur; the CLARA will likely find that the appropriate environment to house this process is unclassified space. By appropriately classifying cleanroom requirements, a facility’s design can be optimized. The facility footprint may be reduced (or a greater manufacturing footprint gained) since fewer airlocks (and rooms) are needed. Classification optimization improves operator comfort and decreases greenhouse gas emissions (lower fan, boiler and chiller energy), water use (cooling towers), gowning requirements and overall operating costs. The key is to judiciously leverage the approach and demonstrate the manufacturing process's quality and safety.
Many (if not most) drug substance manufacturers are not fully leveraging closed processing to improve facility design. In most cases, closed processes that validate closure and have monitoring in place that could be used to evaluate if closure is maintained during processing are still placed in classified clean rooms. This occurs even in newly designed facilities. The reasons as to why aren’t always clear, but the best indication of how far closed processing can be leveraged is from the September 2016 revision of Q7 Good Manufacturing Practice Guidance for Active Pharmaceutical Ingredients from the FDA: “Where the equipment itself (e.g., closed or contained systems) provides adequate protection of the material, such equipment can be located outdoors (4.12).”
Despite growing discussions in this space, the “proper” steps may not be clear to everyone. That’s why a number of biopharma specialists have come together to develop the Closure Playbook.
The playbook provides a roadmap for biopharmaceutical manufacturers and their partners –to support developing, assessing and verifying unit operations. It describes the tools, steps and documents required to adequately assess risk and qualify biomanufacturing facilities that make use of closed-system technologies. The hope is that the biomanufacturing industry can use the closure playbook as a reference to properly leverage closed system technologies in manufacturing facility designs. The playbook itself does not provide commentary on sustainability. However, energy modeling can provide a holistic quantification of savings across the facility when evaluating changes.
This guidance is “not binding,” but it does indicate that, if done properly, API processing equipment housing closed processes that are properly validated and monitored for closure can be located in non-classified spaces – even outdoors. By demonstrating the safety of a closed process and the protection of equipment within the environment, it becomes possible to align with sustainability objectives. When done right, closed processes can mitigate risks, ensure safety and protect the process/product without unnecessarily burdening the environment.
Rob Boulanger is a highly acclaimed and published biopharmaceutical scientist with expertise in process optimization and technology transfer at various production scales. He implements his process and operational expertise in both a design and consulting role by supporting biopharma clients through their various growth stages and has been involved in vaccine production facilities for over 15 years.
Zach Page-Belknap is a driving force for energy efficiency, alternative energy solutions, and sustainable design. His experience centers around the life sciences and biotech industries, with a background in process engineering, detailed design, facility start-up, validation services, and schematic design. Zach is a significant contributor to CRB’s Energy and Sustainability Community of Practice, a member of the International Society for Pharmaceutical Engineering, and has been honored for his outstanding participation and leadership within USGBC’s National Capital Region.