Catherine Casey1, M.Sc., Karl Rogler1, Xhorxhi Gjoka1,
René Gantier1, Ph.D., and Engin Ayturk1, Ph.D.,
1BioPharm Applications R&D
Introduction
Continuous bioprocessing initiatives have accelerated in recent years. The transition from batch to continuous bioprocessing offers numerous advantages, including process time savings and lower capital costs due to smaller equipment, tanks, and tubing sizes. Additionally, hold tanks may no longer be needed between unit operations, which can be especially valuable for facilities with limited manufacturing floor space. Furthermore, reduced system hold-up volumes improve product recoveries and also contribute to the smaller system footprint of continuous bioprocessing systems.
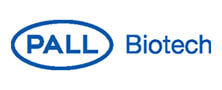
Continuous bioprocessing solutions were initially developed for upstream processes (i.e. perfusion bioreactors), but continuous downstream unit operations have recently progressed as well. One unit of operation that is especially beneficial for continuous bioprocessing initiatives is the ultrafiltration (UF) step, which can be accomplished through the use of Pall’s patented single-pass tangential flow filtration (SPTFF) technology[1,2,3,4]. SPTFF eliminates the conventional TFF recirculation loop and utilizes a staged flow path design, allowing concentrations of 2 to 30X to be achieved continuously in a single-pass through the module. The single pump pass reduces minimum working volume concerns and is ideal for processing of fragile biomolecules. SPTFF modules are also ideal for coupling with other unit operations and enabling a wide range of opportunities for continuous bioprocesses. For instance, they can be coupled with the chromatography step, where the concentrated retentate of the TFF device loads directly onto the column. The lower volumes and higher titers subsequently decrease the chromatography column loading time, while also reducing the tubing and equipment sizes of all other unit operations downstream of the TFF device. The reduced volumes also enable the utilization of disposable, single-use technologies. There is currently a single-use initiative for bioprocessing due to large savings in capital costs, reduced risk of crosscontamination, and elimination of cleaning validation studies compared to processes utilizing stainless steel equipment. However, the single-use space has size limitations; thus, continuous bioprocessing unit operations with SPTFF reduce volumes such that single-use biocontainers and systems can be used in place of stainless steel systems. The main objective of this study is to showcase the versatility of SPTFF technology during processing of various feedstocks and coupled with chromatography steps. In addition to the evaluation of stable operational windows, case studies will also be discussed to show the application benefits at larger scales.
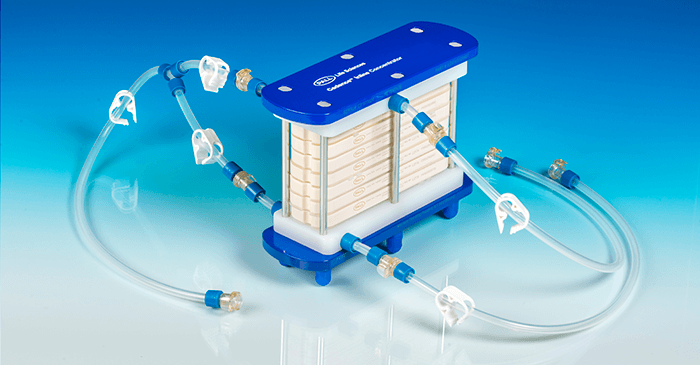